Head, heart, hands.
The Apprenticeshop was founded by educator Lance Lee in 1972 within the complex of the Maine Maritime Museum in Bath, Maine. It became a catalyst for the revival of traditional wooden boatbuilding at a time when the craft and the apprentice way of learning were deemed to be extinct. The program’s design was inspired by the philosophy of Kurt Hahn, who maintained that education should encourage thought and action; not one or the other, but both at once. Lee chose boatbuilding as his medium because he believed in its transformative power. We still believe in this today. The hard skills we teach are the vehicle for exploring personal potential. At its core, the Apprenticeshop is about inspiring personal growth through craftsmanship, community, and traditions of the sea. In line with this mission, hundreds of apprentices, interns, volunteers, and visitors have passed through our doors and left changed, just as hundreds of wooden boats have left the shop floor for new lives on the water.
Make a donation → commission a boat →
Events & Offerings
If you’d like to hear about upcoming events and offerings:
Visit our blog for more stories, updates and announcements.
Preserving maritime craft, building human potential.
The Apprenticeshop is an educational nonprofit organization dedicated to empowering people through building and sailing boats.
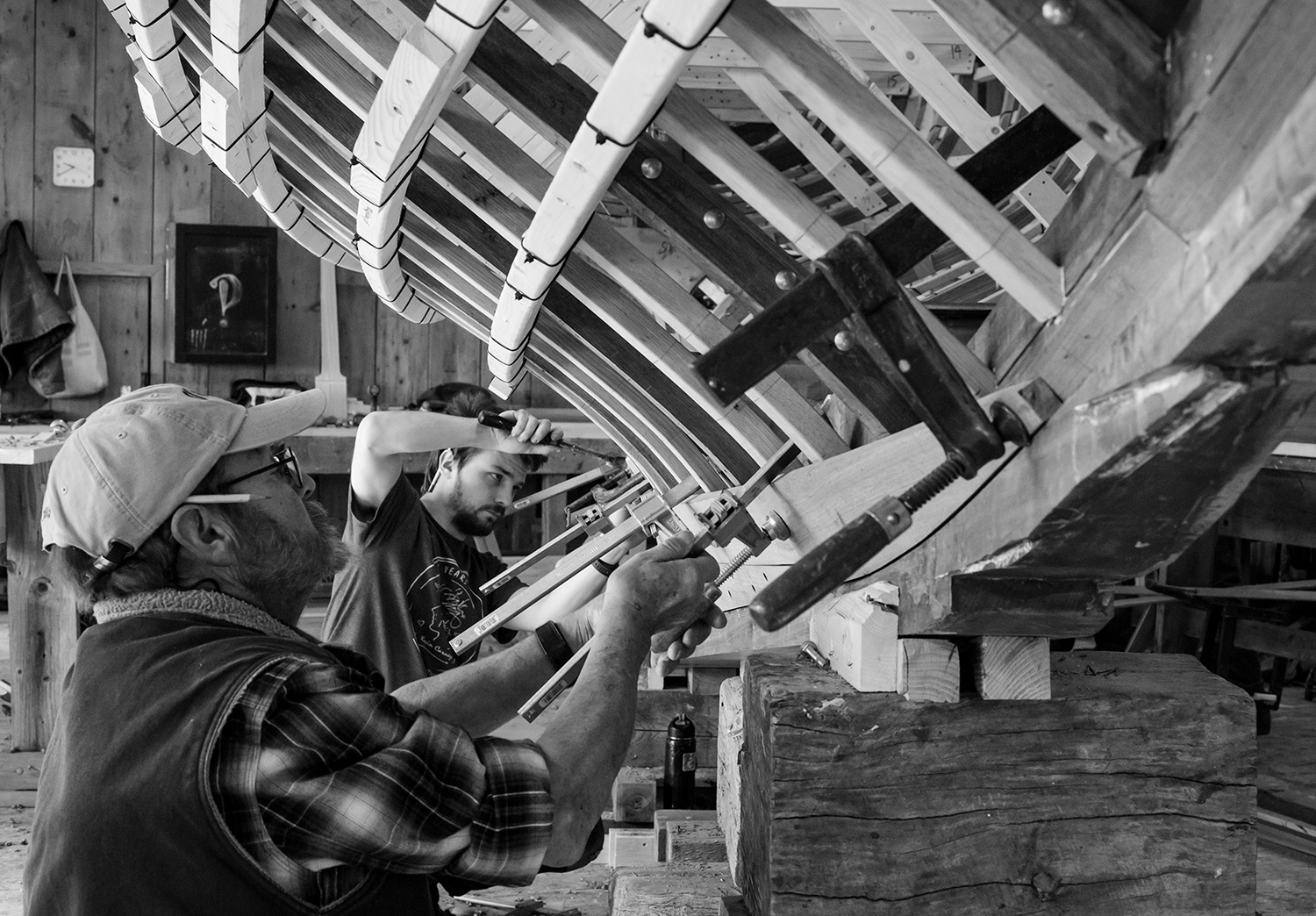